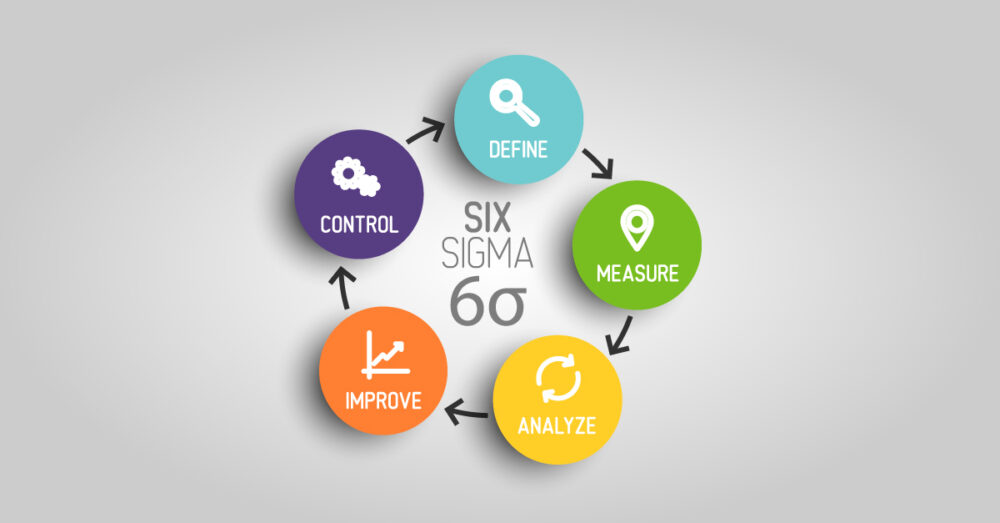
Six Sigma in a non-manufacturing environment
I was in conversation with a couple of people in my network recently about whether 6 Sigma was appropriate in any environment other than manufacturing or logistics. I heard someone say that they worked for a national retailer and Lean 6 Sigma – particularly 5S – was being heavily used in the warehousing and distribution areas of their operations. So in ‘physical’ processes, if you will. In case you don’t know, 5S is a tool used to identify waste and ‘mess’ and eliminate them using the 5 ‘S’ of Sort, Straighten (or Set in Order), Shine, Standardise, Sustain. You have probably used this approach when clearing out the garage, without even realising it. There was a general lack of awareness of other aspects of 6 Sigma and how the methodology might also be used in ‘non-physical’ processes, or transactional, system led processes.
My experience of 6 Sigma
I started my career in a customer service environment. Following the implementation of SAP – R1 and then R2 our customer queries and transaction failures were all over the place. But we didn’t really know where.
We had no management dashboards. We rarely had a data driven conversation and if we attempted it, getting the data together took too long and one person would answer the question with one set of data, versus the next. We didn’t even really know what the business model looked like, where transactions failed and the ‘so what’ impact of those failures – whether it was an internal adjustment or intercompany transfer, or a customer not being billed for products or not paying their invoice.
Enter a new Customer Service Director. Lean Six Sigma trained.
He could not believe the chaos we found ourselves in. He worked with us to build data sets, agree KPIs, build dashboards, and get visibility to process performance.
We started daily reviews with the management team.
We even designed and documented an outline of the business operating model that we could all understand and follow, with clear KPIs associated with each part of the internal and external customer journey across the value chain.
Onward to my own 6 Sigma Black Belt, earned by fixing revenue leakage issues worth 6.7m EUR by correcting pricing, and on to coaching others in their Green Belt projects before becoming an Area Continuous Improvement Manager with a portfolio of initiatives to work on. The importance of defining and measuring the issue and the root cause, as well as the impacts and benefits, allowed our projects to focus – and stay focused – on the valuable 80%.
Of course, there were also the ‘traditional’ Lean 6 Sigma projects in the manufacturing environment using tools such as 5s for example in organising the tool bench and loading areas. We also supported a cancer charity with a Kaizen event focused on short term fixes to organise their fundraising materials and implement processes to track collection boxes.
The overriding importance for me of the 6 Sigma tools and approach in non-manufacturing environments has been to measure process performance across the value chain: focusing on the customer experience or employee experience, using data to identify and then focus on the biggest hitting improvements, validating or arguing against the ‘loudest voice’ with evidence, and measuring and controlling success for sustainable change.
Of course, a series of 6 Sigma projects across the value chain then lead to a set of standard and accepted operating processes. With that, another world of opportunity opens up. No matter what they say, technology change is a whole lot easier when the overall process, process controls and operators of the process are standardised and consistent. A standard process also enables the definition of a set of business performance metrics and a global balanced scorecard that can be compared across teams, service lines and geographies.
Some think that 6 Sigma has had its day. It’s old hat.
I still apply my toolkit every day. And there are some organisations who have reached the maturity of standard processes and visibility of process performance and efficiency. But there are still some who have not.